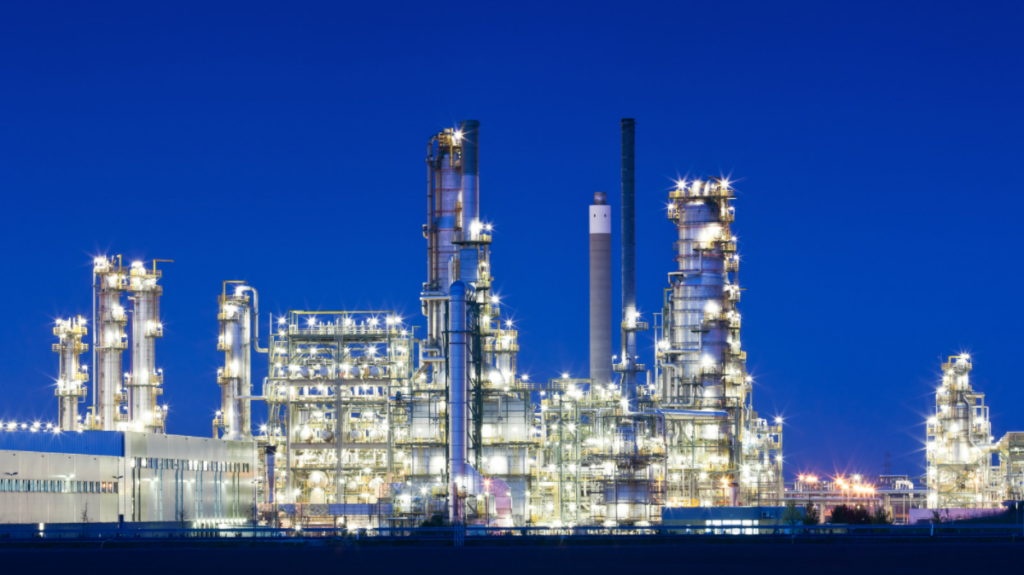
When it comes to flow control, very few industries are as demanding as the chemical industry. Ensuring that the mix of chemical components is accurate is critical for safety, product quality, and minimizing waste. Reducing fugitive emissions within the industry is another crucial element to consider. Keeping chemical leaks from occurring can increase an organization’s overall profitability, reduces the risk of chemical exposure to plant workers, and protects harmful emissions from damaging the Earth’s atmosphere.
Additionally, it is imperative to select valves that can withstand potentially corrosive chemical fluids to reduce downtime to an absolute minimum. With all of this in mind, it is important for chemical plants to select and utilize reliable, field-proven control valves that will assist in keeping their operations running smoothly, while also keeping employees and the environment safe from harmful emissions.
Damage from cavitation
Many of the control valves that are installed within pipelines at chemical plants often sustain internal damage over time due to cavitation. Cavitation damage is a form of hyper-erosion that destroys control valves, which can result in process failures. Cavitation damage occurs when vapor bubbles form and then implode along the pipeline wall. Over time, valves that sustain significant erosion and corrosion damage due to cavitation require maintenance visits and can even bring a chemical plant’s entire operation to a complete halt. When these damaged valves need to be replaced, it makes the most sense to select a product that directly addresses the issue of cavitation as opposed to replacing them with a model that will likely run into the same issue down the line.
Selecting Low-Emissions Technologies
Best available low-emissions technologies in the valve industry can easily be identified by either the International Organization for Standardization (ISO) or the American Petroleum Institute’s (API) standards for fugitive emissions. These 3rd party institutions have a fugitive emissions “A rating” grade that indicates which valves emit 50 parts-per-million of methane, or less, when deployed in the field. A product that holds a leakage rate of 50 parts-per-million leaks 10 times less than a typical valve that does not carry an ISO or API A rating certification. With the health of the planet and best interests for your operation in mind, we strongly urge organizations to strategically select their flow control solutions from valves that fall within this product pool.
eMISSION CONCERNS
The importance for chemical and petrochemical plants to monitor the leakage rates of their valves is more important now than ever. Safety is always the top priority for every chemical plant, especially the well-being of workers. The health of chemical plant employees can easily be compromised if valve emissions are inhaled. For this reason, valve leakage rates needs to be zero. In addition, if a chemical operation does not comply with environmental regulations, it can result in hefty fines. As the requirements for minimizing fugitive emissions will continue to become more strict over time, the need for valves that comply with, and perform well beyond the current fugitive emission regulations increases. Tightening the stem packing of legacy valves is a method that has been used to record lower fugitive emission readings. While this will somewhat reduce the harmful emissions released by the valve for a short period of time, it is not in any way a long-term solution. The stem packing will begin to loosen over time, meaning that your chemical facility unnecessarily runs the risk of exposing end-users, operators, and the atmosphere to these harmful emissions.
The SOLUTION
When exploring control valve options for chemical and petrochemical plants, the Dilating Disk™ Valve should always remain top of mind. It can handle everything from basic and commodity chemicals to polymers and specialty chemicals. Its plug-and-play design also allows you to retrofit your old valves with ease. With its centralized flow path, high-velocity fluids that contain cavitation bubbles are kept away from the pipe walls, leading to significantly less cavitation damage as well as a lower noise output than other control valves. This results in a significant reduction in unwanted downtime and maintenance visits, meaning that your operation can maximize its profitability and overall operational reliability.
The patented stem seal technology of the Dilating Disk™ Valve prevents emissions from escaping from the valve. Its stack of spring energized seals eliminates fugitive emissions and the need for field adjustments and was the key factor in allowing the valve to pass the most stringent emissions ratings of both API 641 and ISO 15848-1 certifications. When the Dilating Disk™ Valve is deployed in your chemical or petrochemical plant’s pipelines, not only are you avoiding unwanted fines, but you are looking out for the health and safety of your workforce and protecting the environment from harmful emissions.
With best-in-class precision control, rangeability, and reliability, chemical engineers trust the Dilating Disk™ Valve in their most critical applications for a wide variety of chemicals, from pure oxygen to Dimethyl Terephthalate. Take control of your critical flow control needs using the next generation of control valves.